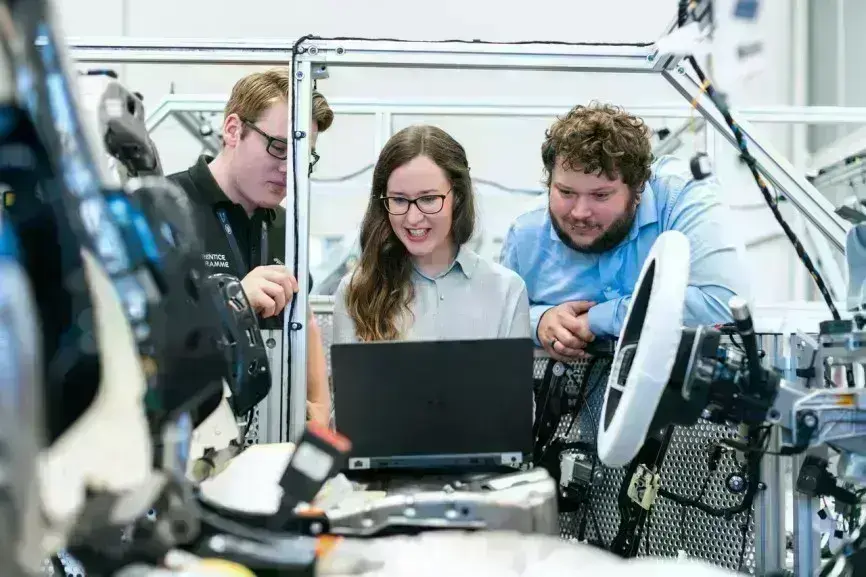
The implications for the future of the infrastructure and urban development (IU) industry: scenario 2
Future global crisis leads to private sector dominance in infrastructure, with a focus on efficient, modular construction and technology.
Factories run the world
Picture this scenario: several decades from now, a global financial crisis strikes that surpasses the damage caused by the 2007-2008 economic downturn. Governments worldwide struggle with the huge debts incurred, and the situation opens the door for cybercriminals to increase their assaults on private and public data networks. Public trust is eroded as governments fail to solve these problems promptly.
Gradually, the private industry assumes tasks – including providing defence and infrastructure – which were solely observed by the public sector. Following government agency blessings, corporations utilise business principles to solve societal issues.
As time goes on, prosperous financial times make their return. A new profit motive for countries ensures they adopt lean principles and combine these with technological developments – particularly in the manufacturing sector. This global prosperity comes with drawbacks. It impacts the environment and certain social groups, while internet-free closed data systems – used to protect against cyberattacks – limit international cooperation.
A boom in construction
As the economy flourishes, there’s a boom in the construction of office, commercial, and industrial buildings, along with energy and transportation infrastructures being developed to handle economic demand. As cyberattacks effectively close down online activities like remote work and e-commerce, businesses require additional office space and retail premises.
Due to society’s alignment with business principles, the priority is new construction projects completed as quickly and cheaply as possible. This leads to extra features and exceptional design being secondary considerations.
How the IU value chain adapts to construction demands
Construction must be cost-effective and fast, so the IU industry must adopt lean principles. These must be combined with advanced manufacturing processes to ensure assets can be produced on a large scale via mass-customised and prefabricated modules.
Whether it’s bathrooms or bridge parts, all built assets are produced from set modules found in design libraries, and designs are standardised as much as possible for maximising efficiency. Despite the normalisation of modules, mass customisation and advanced manufacturing techniques ensure that all assets match customer requirements.
Construction work mostly happens within prefabrication factories. By combining traditional production techniques with advanced manufacturing techniques – like 3D printing – factories can produce extensive quantities of customised modules swiftly. Once shipped to building sites, the construction work primarily involves assembling the modules. Due to the ‘plug-and-play’ aspect, tasks can be done quickly and with fewer workers.
Because of how they’re standardised, maintenance for modules is easy to duplicate and efficient. Digital models of all assets will also include information about repair and replacement costs, and this helps O&M companies settle on the most cost-effective approach when issues arise with modules.
Why suppliers benefit the most
With lean principles, mass customisation, and prefabrication being adopted on a large scale, the focus of the IU industry has changed. Instead of businesses being built around projects, they are now built around products.
As a result, suppliers benefit the most from the change. By distributing complete building modules, suppliers take control of aspects of the IU value chain formerly operated by contractors, O&M providers, and design and engineering companies. The latter particularly lose out as there’s less demand for assets created from scratch. Contractors are potentially relegated to low-value module assembly work on-site. At the same time, O&M providers miss out on business because low-cost modules can be replaced with as much ease as going through with repairs.
The IU industry will be dominated by those who provide end-to-end integration, covering everything from design to O&M. Industry leaders will also find it easy to raise money from investors and promote construction activity. This is because standardised processes, consistent costs, and reliable scheduling information make it much easier to predict cash flow.
Logistics requirements and integrated systems supply new business opportunities
When factories run the world, this opens the door to various new business opportunities. This includes those who decide to sell platform-based integrated systems. As construction is primarily focused on prefabrication and modularisation, IU organisations can utilise platform strategies to begin selling integrated systems alongside structural elements. These systems can expand into electronics, lighting, plumbing, and mechanical equipment subsystems.
Even today, this approach is already being adopted by BSB. They sell standardised floor plates, tile and laminate flooring, and pre-fitted steel frames with wires and pipes. To pick the ideal flooring combination for their needs, clients make their choices via a simple customisation menu. BSB has also demonstrated how module suppliers can overcome logistical limitations with a certain approach: franchising.
Even in a future world run by factories, it is not feasible for a company to transport sizeable building modules across long distances. This logistical situation would place a severe strain on financial viability. By franchising, however, various areas can be suitably covered from a logistics point of view. The more franchises that can care for the manufacturing and distribution of modules, the less worry about transportation concerns.
Speaking of logistics, this plays an integral role in a factory-run world. Rather than transporting low-value construction items like lumber and bricks, logistic companies have to deal with high-value prefabricated modules. These modules must be delivered on time, and logistics suppliers will typically have the added headache of scheduling deliveries from multiple factories to provide construction sites with all requested assets. Due to the complexity of the task, logistic businesses need to possess refined software solutions that can track and automate tasks.
The future (and present) need for software solutions
Even in a world where factories control the IU industry and online activities are restricted, technology and software solutions are still essential components. It is needed to coordinate activities effectively, complete the production of modules, and much more.
In today’s world, it is more vital than ever for IU companies to adopt technology and remain up-to-date with on-demand software services. They assist with everything from automating tasks to eliminating the possibility of human errors compromising projects.
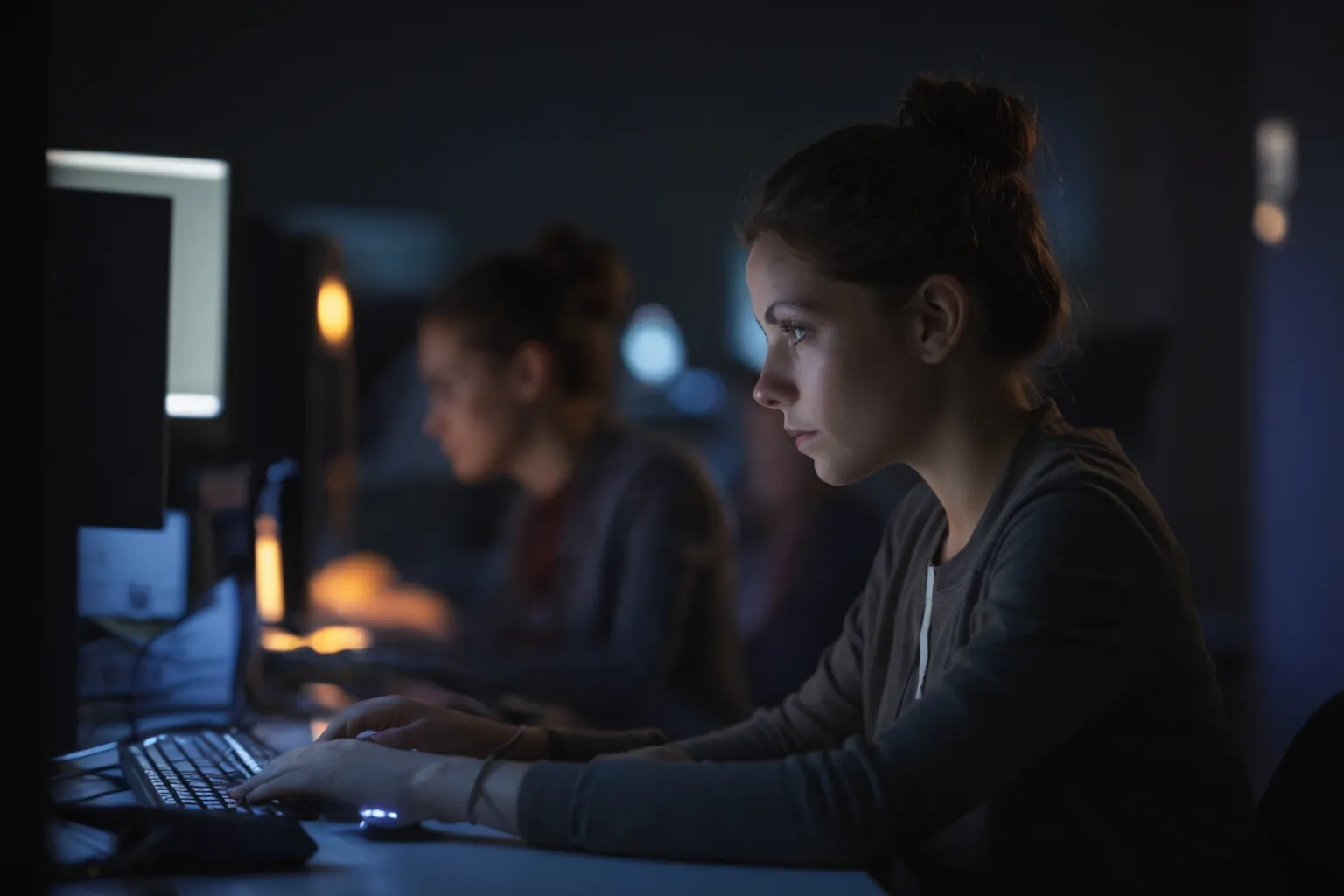
Contact us.
If you need a partner in software development, we're here to help you.
We will respond to your enquiry immediately.